An Introduction To Fabric Grouping
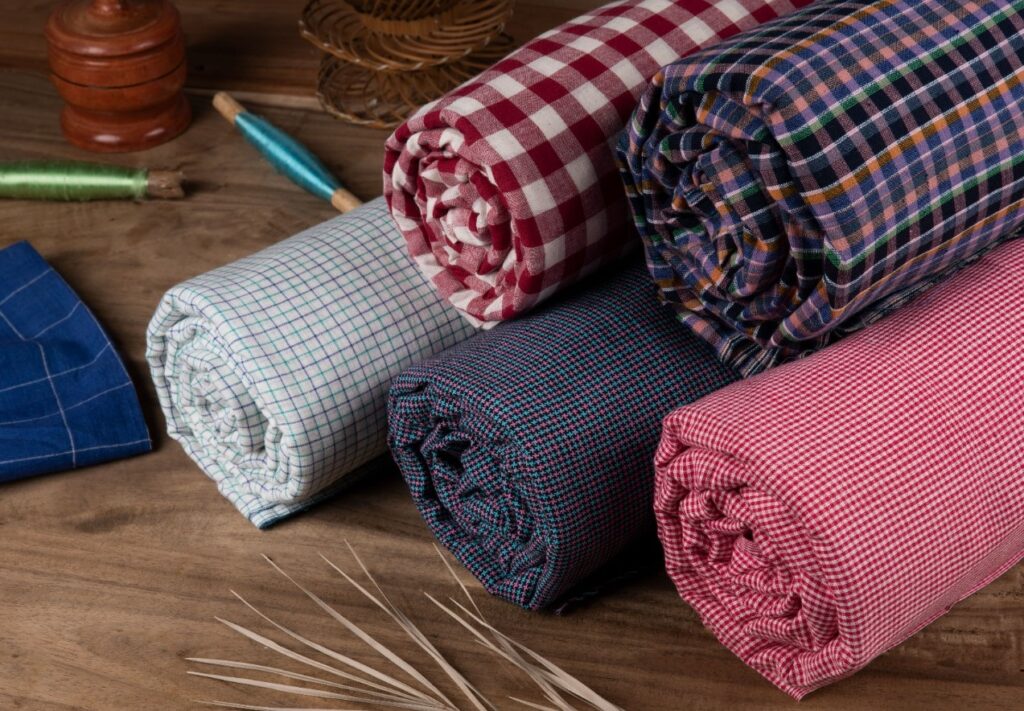
Fabric grouping is the procedure where special rolls of material are separated and grouped based on their specs and other bodily properties. The primary motive of material grouping is to maximize material usage and minimize slicing time. Ordering bulk fabrics means getting several rolls of cloth with varying lengths, sun shades, widths, or even shrinkage ranges. Fabric grouping guarantees top-quality fabric utilization and reduces room overall performance to avoid wastage. Click here
Why is Fabric grouping vital?
Fabric grouping is considered one of the key elements regarding fabric utilization. Different fabrics want to be treated differently to get regular outcomes. These fabrics also react otherwise for the duration of the garment-making technique. This increases the need to institution bulk fabrics based on their physical traits before processing them into clothes.
Here are a few vital reasons each clothes manufacturing facility ought to don’t forget material grouping-
- It facilitates assess the first-class of the cloth, especially if it’s miles sourced from distinctive suppliers
- Similar Fabric while grouped, resulting in faster processing and quicker flip-around time
- It allows for decreasing the wastage of cloth for the duration of the processing time
- Bulk materials may have coloration versions, which can be detected at some stage in fabric grouping.
- It allows employees to recognize the Fabric’s reaction to numerous processing steps and plan as a consequence. For ex-, a few materials may additionally reduce more or much less in the course of the cloth washing method
- It helps employees create a marking and cutting plan for every man or woman’s cloth roll, reducing the possibility of blunders and, thereby, wastage.
Thumb Rules For Fabric Grouping
Garment factories usually place bulk orders for Fabric, once in a while, from different assets. These fabrics want to be grouped, relying on their physical homes. This enables less wastage of material and quicker processing time. When the factory gets material rolls, they may be segregated primarily based on the following homes-
By shade and shade-
A piece of garment with different sun shades is not an awesome-pleasant product. The shade version is a clear indicator of a faulty/negative-first-rate garment. This explains the need for material grouping primarily based on color, preventing the mixing of various sunglasses’ garment components.
By fabric shrinkage–
This can only be prevented for some fabrics, precisely knitted fabrics. Cutting Fabric without considering the shrinkage issue may cause your garment measurements to go for a toss. It is vital to recognize the fabric shrinkage percent of a material roll so that it may be factored into the design after you chop the cloth. This will leave room for a few quantities of shrinkage once the garment is washed, that’s unavoidable in maximum cases.
By fabric width-
Fabric rolls obtained by way of the factories typically vary in width. This distinction in width desires to be segregated for this reason. With the equal-width fabrics grouped, assembling the markers for the reducing technique is more spartan. This affects minimal wastage and maximum material usage. Factories can also make use of excess Fabric for the production of other clothes. This is one of the essential blessings of fabric grouping based on width.
For this purpose, most factories have a sure system for grouping the fabric rolls received through them. Factories perform the subsequent sports to test for material quality, and comparable fabrics are grouped after the following checks are performed-
- Measuring the material width
- Fabric thread count number and weight check
- Fabric shrinkage test on distinctive cloth rolls
- All fabric rolls were checked for coloration versions
- Testing the high-quality of the material
- Performing the stretch check to evaluate cloth elasticity
The fabric rolls with comparable characteristics are then grouped and brought for similar processing, which involves a marker and slicing manner. After segregating, the garment factory has to take care of the grouped material cautiously. Each grouped cloth needs to be carefully labeled. Then, markers should be set in step with the cloth width. Only then can material wastage be minimized.
Reducing Time In The Fabric Grouping Process-
Fabric grouping in garment factories is accomplished in two methods-
Manual grouping
In this procedure, the material is grouped manually and segregated according to its bodily characteristics. These businesses are then processed. For this, the manufacturing unit people should set the markers and reduce plans in step with each institution. This will increase guide hard work and processing time of the garments, and there are excessive chances of errors.
Automated grouping-
In this manner, computerized machines locate the cloth period and modify the markers and cutters. Though this manner is quicker, it requires high automation, which might need to be revised for small manufacturing facility owners. Whether manual or automatic, fabric grouping is significant in garment factories.
Some of the characteristics of efficient cloth grouping are-
- It has to be easy to be followed with the aid of the manufacturing facility employees.
- It needs to reduce fabric wastage drastically
- It needs to be time-saving and grow the cloth’s turnaround time.
- It must only comprise a few markers to bring about an extended workload for the workers effectively.
- With so much importance given to material grouping, maximum of the time, garment factories may additionally both have the resources or the time to test every cloth roll that comes from the fabric mill. This tedious process will now not simply result in a waste of time but will even destroy material as nicely.
In such cases, garment producers should rely upon the material turbines to provide the necessary facts concerning the cloth rolls supplied. Fabric turbines must put together high-quality reviews of every cloth roll synthetic through them. These fabric best reviews contain critical statistics regarding the fabric’s pleasantness, shade, fabric thread matter, material stretch remember, material shrinkage, and many others. Garment manufacturing unit proprietors can rely on these reviews to organize the fabric. This saves much time and effort for garment manufacturing unit owners, who might otherwise need to undergo the tedious fabric testing method.
Other approaches to material usage-
The cost of material constitutes 60%-70% of the overall garment cost. Fabric is the maximum sizable and fundamental uncooked fabric for a clothes manufacturer. Therefore effective utilization of its top essential aid will result in a growth in earnings margins. Though fabric grouping is one way of lowering cloth wastage, there are many other ways to boom fabric utilization and financial savings for the producer. Here are some ways in which most cloth usage can be done-
Keeping a report of the material ordered-
Keeping a correct file of the quantity of cloth ordered and the amount of fabric used every time will assist in reducing fabric wastage and additionally help avoid repetitive or extra buy of materials than necessary
Planning right slicing and marker putting-
This is very vital when it comes to powerful fabric utilization. Proper reduction and marker placing will assist in making the fabric laid out pleasant. This step is essential to avoid fabric wastage, whether manually or via machines. Factory people need to observe maximum marker duration and height settings for maximum cloth utilization
Segregating material rolls by coloration and width-
As stated above, fabric grouping has to be finished earlier than planning the slicing process to institution similar fabric and treat them for this reason. This will assist workers in setting a couple of markers for every material type, reducing system waste.
Quality check of material earlier than reducing procedure-
A thorough, high-quality look at the fabric will ensure that it’s miles even without any defects or cuts. This will reduce ugly surprises for the duration of the reducing system, as a way to be too late. This could impact the niceness of the clothes.
Purchase of low-shrinkage cloth-
Fabric that tends to reduce can damage the manufacturing process. It results in low-excellent clothes that are different in size. Material that shrinks also requires extra wash earlier than the cutting system, growing staffing and turnaround time.
Ways of utilizing the extra fabric-
Excess cloth can be applied in different methods. If the right cutting plan is applied, the extra fabric can be used properly to manufacture garments in smaller sizes. The manufacturing facility owner can use many different innovative thoughts to monetize the excess material left.